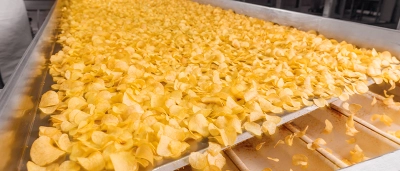
Vibratory conveyor systems have gentle handling, hygienic design and versatility. Making them an alternative for the food industry for goods such as fruit & vegetables, nuts, baked goods, grains and many more.
Applications of Vibratory Conveyors in the Food Industry:
Application | Description | Common Food Types |
---|---|---|
Feeding/Transferring | Moving products between processing stages. | Vegetables, nuts, baked goods, grains, meat portions. |
Screening/Sorting | Separating by size, weight, or shape. Often includes mesh screens or air knives. | Frozen foods, snack foods, nuts, grains. |
De-watering | Removing excess water or oil from washed or fried products. | Leafy greens, fruits, fried snacks. |
Spreading/Aligning | Distributing products uniformly for further processing or packaging. | Biscuits, cookies, meat slices. |
Cooling/Drying | Using ambient or forced air as product vibrates. | Cooked pasta, steam vegetables, hot snacks. |
Accumulation/Buffering | Holding product temporarily in line before the next stage. | Packaged foods, produce. |
Inspection | Integrated with vision systems or manual inspection areas. | Packaged goods, prepared meals. |
Benefits of Vibratory Conveyors in Food Applications:
Benefit | Why it matters |
---|---|
Hygienic Design | Easy to clean, made from food-grade stainless steel. |
Low Maintenance | Fewer moving parts than belt or roller conveyors. |
Gentle Handling | Minimises product breakage or damage. |
Flexible Layout | Can be straight, curved, inclined or declined. |
Integrated Functionality | Can combine conveying with de-watering, screening, or alignment. |
Quiet Operation | Low noise levels compared to mechanical alternatives. |
Functionality - Where Vibratory Conveyor Systems are used in the Food Industry:
Food Sector | Use Cases |
---|---|
Produce Processing | Washing, de-watering, sorting fruits and vegetables. |
Snack Food Manufacturing | Conveying, seasoning, cooling, and packaging potato chips, nuts, crackers. |
Meat & Poultry | Portion handling, screening, deboning lines. |
Frozen Foods | Handling delicate items like peas or berries without damage. |
Bakery | Transporting dough pieces, cookies or pastries. |
Dairy | Moving cheese curds or slices in hygienic conditions. |
A key component of a vibratory system is the leaf spring setup. Traditionally, steel leaf springs have been used but there are substantial benefits for using composite leaf springs as an alternative. Composite leaf springs offer lighter weight with an increased strength-to-weight ratio, excellent corrosion and fatigue resistance. Improved design flexibility and vibration dampening with reduced maintenance. See more below.
Why use Composite Leaf Springs vs Alternative Materials (Steel)
Property | Composite Leaf Springs | Steel Leaf Springs |
---|---|---|
Weight | Up to 70% lighter than steel. Reduced unsprung mass improves ride and fuel economy. | Heavier, increasing vehicle weight and reducing fuel efficiency. |
Strength-to-weight Ratio | Very high - tailored fibre orientation optimizes load paths. | Lower compared to composites: overdesigned to compensate. |
Corrosion Resistance | Excellent - inherently resistant to moisture, salt and chemicals. | Prone to rust; requires protective coating and maintenance. |
Fatigue Life | Long fatigue life due to no initiation of micro-cracks like in metals. | Susceptible to fatigue cracking over time, especially under high cyclic loads. |
Design Flexibility | Easily molded into complex shapes for space or performance gains | Limited to uniform cross-sections and simple geometries |
Tailored Stiffness | Customisable stiffness by fibre type, layup angle, and matrix composition | Fixed by material dimensions and alloy choice |
Vibration Damping | Superior damping reduces noise, vibration, and harshness (NVH) | Poorer damping – transmits vibration to chassis |
Thermal Conductivity | Low – reduces heat transfer to other components | High – can transfer heat which may affect adjacent systems |
Manufacturing Cost | Higher material and tooling costs | Lower – raw material and fabrication methods are well established |
Production Time | Longer cycle times due to curing and layup processes | Faster – well-established forging and stamping processes |
Recyclability | Limited (especially thermoset composites); some thermoplastic options improving | Fully recyclable through remelting and forming |
Reparability | Difficult – usually requires full part replacement or specialist repair | Easier – can be welded or re-arched |
Environmental Exposure Durability | Resistant to UV, moisture, and chemical degradation (especially with additives) | Requires regular maintenance to preserve performance |
Lifecycle Cost | Often lower due to reduced maintenance, longer life, and weight savings | Lower initial cost but higher over time due to wear, corrosion, and weight penalty |
Application-Specific Use | Ideal for performance vehicles, EVs, off-road equipment, and vibratory systems | Common in heavy vehicles, trucks, and cost-sensitive applications |