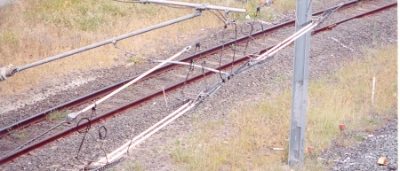
What is an Insulator?
An insulator is a material that restricts or inhibits the flow of electricity, heat, or sound. Even though the engineering plastics that Dotmar specialise in are thermal and sound insulators, our materials lend themselves to electrical insulation.
These materials have high electrical resistance, which means they do not allow electrons to flow easily through them, as well as high dielectric strength, i.e. the resistance to breaking down by “sparking through”.
Insulators are vital in electrical systems to prevent the loss of energy through unwanted conduction and to ensure safety by containing and directing the flow of electricity.
Benefits of Plastic insulators
- Resistance – engineering thermoplastics tends to volumetric and surface resistance of in the order of 1012 to 1014 respectively.
- Dielectric Strength – traditional electrical insulating materials tend to have dielectric strength of approximately 12 kV/mm, while engineering thermoplastics commonly range from 15 kV/mm to 45 kV/mm.
- Chemical Resistance – For electrolysis applications (or similar) where chemicals are present, thermoplastics, such as Polystone P, Trovidur EC-N, and Tetron S, have excellent chemical resistance and generally prove to be an ideal solution to solve for electrical insulators in chemical environments.
- Temperature Resistance – Materials such as Tetron S & Ketron PEEK 1000, offer not just high electrical resistance and dielectric strength, but also allows for continuous operation up to 2600C, and short-term temperatures of up to 3100C.
Dotmar has qualified engineers that can provide direct support with plastic insulator material selection, including conducting calculations for thicknesses required to resist breaking down by “sparking through”.
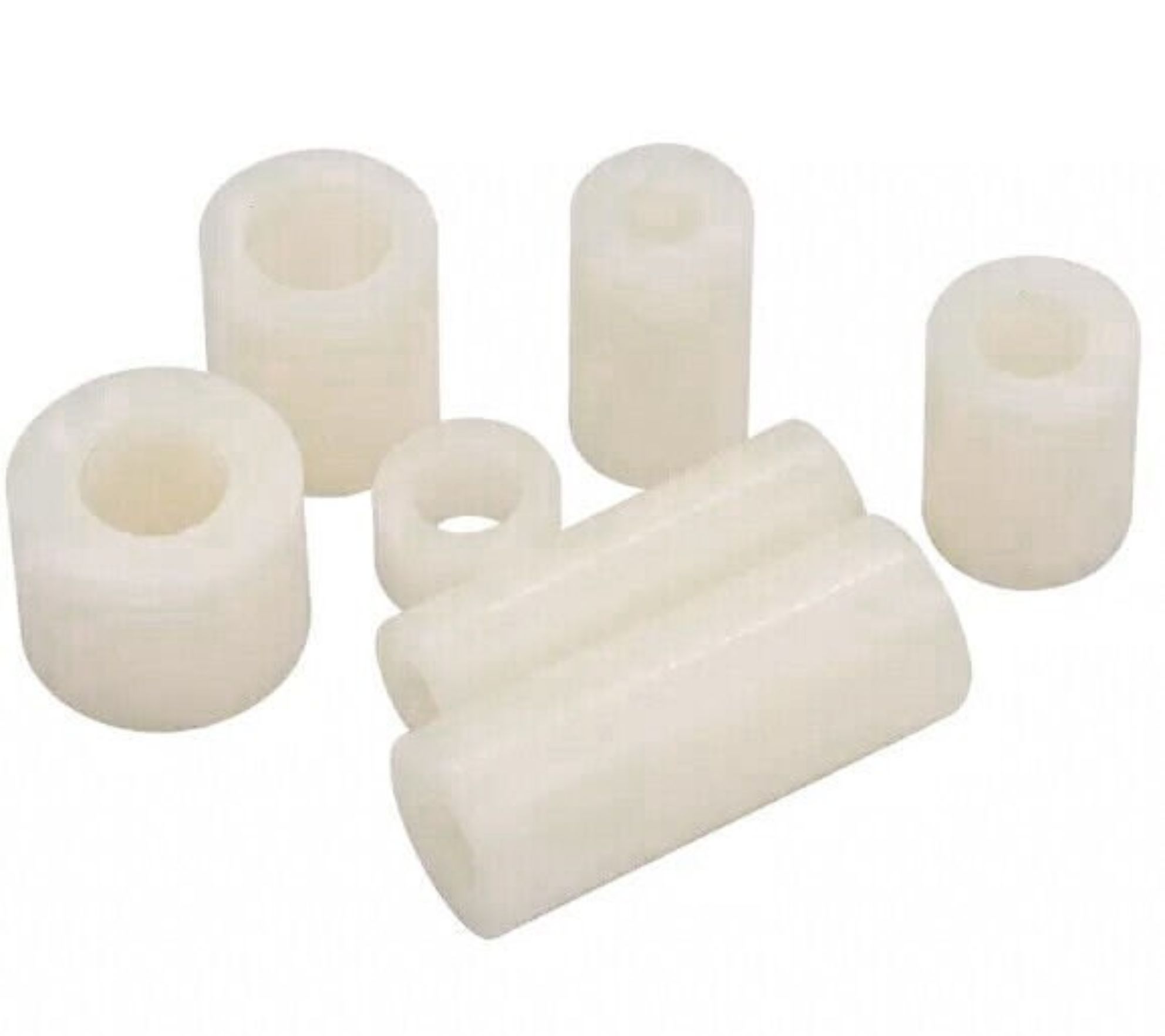